There are many types of ceramic sintering processes. From the perspective of phase changes, one type of sintering process in which the powder is not completely densified in the solid phase is called solid state sintering.
We can divide the solid state sintering into unit system solid state sintering and multi-component system solid state sintering. Solid state sintering refers to densification without any liquid phase generation. This kind of complete solid state diffusion is difficult to obtain a product with a high degree of densification.
Solid state sintering mechanism
We can generally divide the solid state sintering into three stages. In the initial stage, it is mainly a change of grain shape. In the middle stage, it is mainly a change of pore shape. And in the final stage, it is mainly a reduction of pore size. We can see the arrangement process of grains during sintering in the figure.
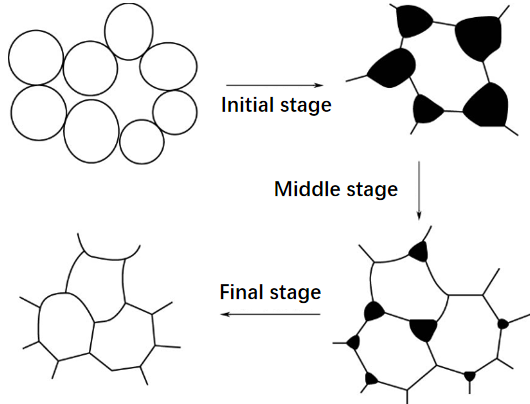
In the initial stage, the shape of the grains changes, and they will form neck connections between each other. The pores gradually transition from the original columnar through-state to the continuous through-state. Its function can increase the density of the blank by 1%~3%.
In the middle stage, all grains are in contact with the nearest neighboring grains and diffuse through the lattice or grain boundary. The material between the grains is migrated to the neck surface, resulting in sample shrinkage, and the pores change from continuous channels to isolated states. When the pore channel becomes narrower and cannot be stabilized and decomposed into closed pores, this stage will end. At this time, the sintered sample can generally reach a relative theoretical density of about 93%.
In the final stage, the transition from pore isolation to densification is completed. At this stage, the pores are closed, mainly at the grain boundaries. During the grain growth process, the pores continue to shrink. If the pores contain gas that is insoluble in the solid phase, the internal gas pressure will increase during contraction, and eventually, the contraction will stop and form closed pores.
The mechanism of the initial stage of sintering is based on the double-sphere model.
Assuming that the morphology of the sintered powder is a regular sphere, we can regard the entire powder body as the sintering between two particles. As the sintering proceeds, the contact points of the spheres begin to form a neck and gradually expand, sintering into a whole. The growth rate of the neck formed by the two particles represents the kinetic relationship of the entire initial sintering. In all systems, the surface energy is the same as the driving force. Different mass transfer mechanisms and different neck growth methods during sintering result in different results.
Back to SINTERING TECHNOLOGY
You might be interested in: