What is sintering technology?
The sintering technology process is a process in which powdered materials are subjected to a high temperature below the melting point, through the mutual bonding of particles between the embryos and the transfer of materials, the elimination of pores, the shrinkage of volume, and the improvement of strength. Gradually, it becomes a densification process with a certain geometric shape and a solid whole. The purpose of sintering is to turn powdered materials into dense bodies.
People have long used this process to produce ceramics, powder metallurgy, refractory materials, ultra-high temperature materials, etc. Generally speaking, after the powder is formed, the dense body obtained by sintering is a polycrystalline material. Its microstructure is composed of crystals, glass, and pores. The sintering process directly affects the grain size, pore size, grain boundary shape, and distribution in the microstructure, and thus affects the performance of the material.
Microscopic definition: There is mutual attraction between molecules (or atoms) in the solid state. The process of heating so that the particles obtain enough energy to migrate so that the powder body produces particle bonding, strength, densification, and recrystallization is called sintering.
Sintering technology history
Sintering has a history of thousands of years. In the ancient civilization of Mesopotamia, people began to use clay to prepare bricks in open-pit mines. This is the beginning of the application of sintering in practice, which can be traced back to 6000 BC.
In 3000 BC, the ancient Egyptians used sintering technology to prepare metal and ceramic products. At the same time, the Incas in South America also prepared yellow platinum jewelry and other products through sintering.
From 1920 to 1950, technical workers and scientific researchers gradually introduced sintering technology from practical experience to the field of solid science. To make it easier for people to understand the sintering process, Frenkel et al. used a mass transfer mechanism to explain the basic phenomena produced in sintering.
With a basic understanding of the basic phenomena that occur during sintering and the important parameters that control sintering, people have become interested in the thermal activation process during sintering. We know that there are many ways to activate heat during sintering. Among which is the most widely studied in recent years is the activation of the sintering process by electric current. As early as the 1930s and 1940s, some patents mentioned that pulse current helps promote the sintering of powder materials or metal connecting materials. In the 1960s and 1970s, this statement was confirmed by scientists in the United States, Japan, and other countries.
What are the factors that affect sintering?
- The influence of material parameters on sintering
During the sintering process, such as ceramic products, the parameters related to the material have a greater impact on the densification of the powder and the process of grain growth. Including particle size, powder structure, and agglomeration, particle shape, particle size distribution, additives. - Sintering temperature and time
Increasing the sintering temperature is beneficial to mass transfer such as solid phase diffusion. However, too high a temperature will promote secondary crystallization and deteriorate the material properties. The low-temperature stage of sintering is mainly surface diffusion, and the high-temperature stage is mainly volume diffusion. Low-temperature sintering for too long is not conducive to densification and deteriorates the performance of the material. Therefore, high-temperature short-time sintering is usually used to improve the density of the material. - Sintering atmosphere
Sintering in the air will cause vacancies in the crystal and cause defects. Therefore, the atmosphere should be selected for sintering different matrix materials. The influence of the atmosphere on sintering is very complicated. For general materials such as TiO2, BeO, Al2O3, etc., oxygen can escape directly from the crystal surface when sintered in a reducing atmosphere, forming a defective structure, which is conducive to sintering. Non-oxide ceramics are easily oxidized at high temperatures, so they are sintered in nitrogen and inert gases. PZT ceramics require atmosphere sheets or atmosphere powders for closed sintering to prevent the volatilization of Pb. - Molding pressure
The molding pressure of the green body is also crucial to the performance of the material. The greater the molding pressure, the tighter the contact between the particles in the green body, and the smaller the diffusion resistance during sintering. Excessive molding pressure will cause brittle fracture of the powder, which is not conducive to sintering.
Classification of sintering technology
The classification of sintering technology mainly includes the following methods:
Classification by pressure
Including normal pressure sintering and pressure sintering.
Normal pressure sintering:
Normal pressure sintering is also called pressureless sintering. That is, the material is sintered under atmospheric pressure without pressurization. It is the most commonly used sintering method. It includes normal pressure sintering under air conditions and normal pressure sintering under certain special gas atmosphere conditions. During the normal pressure sintering process, the green body is not subjected to external pressure and only undergoes heating under general gas pressure to transform from an aggregate of powder particles into a grain bond. This method has a high sintering temperature, high requirements for the furnace, and a relatively large waste of energy.
Pressure sintering:
During the sintering process, the green body is subjected to external pressure. Mechanical pressure or gas can be used as a method of transmitting pressure. Including hot pressing sintering, gas pressure sintering, hot isostatic pressing sintering, etc.
Hot pressing sintering:
Refers to the process of sintering powder to obtain a dense block under the simultaneous action of mechanical pressure and temperature. Hot pressing sintering can make heating sintering and pressurizing forming proceed at the same time. The green body is continuously subjected to pressure at high temperatures. The powder raw material is in a thermoplastic state, which is conducive to the flow and diffusion of the material. The external pressure offsets the deformation resistance and promotes the contact between the powder particles.
Atmosphere pressure sintering:
Atmosphere pressure sintering refers to the method of sintering the ceramic green body at high temperatures under nitrogen or another inert atmosphere with a certain pressure. This method can be used to prepare ceramics with high density and relatively complex shapes. This method was invented in the United States and Japan in the mid-1970s and is mainly used to prepare high-performance SiN ceramics. It uses high-pressure nitrogen to inhibit the decomposition of SiN. So that silicon nitride ceramics with high performance and high density can be obtained at a higher temperature.
Hot isostatic pressing sintering:
The powder compact or the powder in the package is placed in a high-pressure container. The powder is subjected to high temperature and balanced pressure and sintered into a dense part.
Classification by Atmosphere:
It is divided into ordinary sintering, hydrogen sintering, vacuum sintering, etc.
Classification by the internal state of the green body:
Including solid state sintering, liquid phase sintering, gas phase sintering, activated sintering, reaction sintering, etc.
Solid state sintering: The process of densifying the sintered body by mass transfer without producing a liquid phase during the sintering process.
Liquid phase sintering: The sintering process with the participation of the liquid phase.
Activated sintering: Including physical activated sintering and chemical activated sintering. The former promotes sintering by periodically changing the sintering temperature and applying mechanical vibration, while the latter involves chemical reactions to enhance the densification process.
These classification methods reflect the different physical and chemical conditions in the sintering process, which have an important impact on the performance of the final product.
What are the types of furnaces for sintering technology?
Sintering furnaces can be divided into different types according to the atmosphere and vacuum used in the furnace, as well as the structure and operating properties of the furnace.
Continuous sintering furnace
The compact passes through the furnace chamber of the preheating section, high-temperature section, and cooling section of the furnace at a certain speed. This furnace has the advantages of large production volume, uniform product quality, high thermal efficiency, and convenient operation. Common continuous sintering furnaces include mesh belt furnaces, walking beam furnaces, and push rod furnaces.
Mesh belt furnace: Usually no firing boat is required, heating is uniform, operation is simple, and the degree of automation is high. It is suitable for the production of powder metallurgy mechanical parts.
Walking beam furnace: The compact is pushed into the furnace for sintering through the walking beam.
Push rod furnace: The compact is loaded in the firing boat or on the pad and is pushed into the furnace for sintering by mechanical or manual transmission.
Batch sintering furnace
At a certain time interval, the furnace is opened, the compact is put into the furnace, sintering and the sintered parts are taken out of the furnace. Common ones include vacuum sintering furnaces, multi-atmosphere vacuum sintering integrated furnaces, low-pressure sintering furnaces, hot pressing sintering furnaces, hot isostatic pressing sintering furnaces, plasma pulse sintering furnaces, microwave sintering furnace, etc.
Vacuum sintering furnace
Sintering under negative pressure in the furnace is called vacuum sintering. There are intermittent vacuum sintering and continuous vacuum sintering. Continuous vacuum sintering is rarely used because the furnace is more complicated, the vacuum degree is not guaranteed, there is no way to pass gas, the sintering process curve is not easy to adjust, etc. Intermittent vacuum sintering has a special vacuum sintering furnace, equipped with a matching dewaxing furnace.
Multi-atmosphere vacuum sintering integrated furnace
The appearance of the multi-atmosphere vacuum sintering integrated furnace is not much different from that of the ordinary vacuum sintering furnace, mainly adding a process gas system, a forming agent removal system, and a product rapid cooling system.
Sintering HIP furnace
After the densification process is completed, a process of pressurizing and keeping warm at the sintering temperature is added, which is called gas pressure sintering. It is called gas pressure sintering because the pressure is transmitted by gas, usually argon. The pressure is generally 1~10MPa. This pressure range is much lower than hot isostatic pressing, so it is also called low-pressure sintering.
Hot pressing sintering furnace
Hot pressing is a process that simultaneously carries out pressing and sintering. Sintering under external pressure can complete the sintering process quickly, and the sintering temperature is also lower than that of ordinary sintering, which is the activated sintering method. Therefore, the growth of carbide grains is much smaller than that of ordinary sintering, and it is also more dense.
Spark Plasma sintering furnace
Spark Plasma Sintering (SPS), also known as “Field Assisted Sintering Technology“, “Direct Current Sintering“, or “Fast Hot Pressing Sintering“. SPS combines plasma activation, hot pressing, and resistance heating. It has the advantages of fast heating speed, short sintering time, and uniform grains. This is conducive to controlling the fine structure of the sintered body, and the obtained material has high density and good performance. It is a new technology for material preparation that is fast, low-temperature, energy-saving, and environmentally friendly.
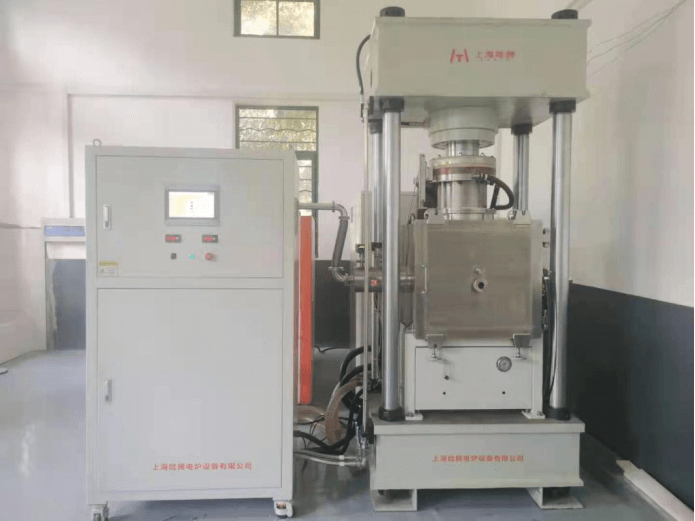