Hot pressing sintering is a method of sintering a blank by applying pressure at high temperatures. It is also a new process that can simultaneously complete the forming and firing of the blank. We widely use this method in powder metallurgy and high-temperature material industries. For refractory non-metallic compounds (such as borides, carbides, etc.) and oxide ceramic materials, they are not easy to press and sinter. The sintering effect of hot pressing is remarkable. As a new firing method, hot pressing sintering has gradually become an important way to improve the performance of ceramic materials and develop new ceramic materials.
The densification process of sintering
During the pressure sintering process, the deformation of the powder body is the deformation under the simultaneous action of stress and temperature. Complete the material migration through various mechanisms such as dislocation slip, climb, diffusion, diffusion creep, etc. Generally, we can divide this type of pressure sintering into two stages. Ashby divides these two stages into the pore connection stage and the isolated pore stage.
In the first stage of pressure sintering (also known as the initial stage of sintering), the application of stress first causes plastic yielding in the contact area of the particles. Then, it formed a power exponential creep zone in the increased contact area, and various creep mechanisms led to material migration. At the same time, atoms or vacancies inevitably undergo volume diffusion and grain boundary diffusion. Dislocations in grain boundaries may also climb along grain boundaries, leading to grain boundary sliding.
In the second stage of pressure sintering (also known as the end of sintering), the above mechanism still exists, but the holes become isolated closed holes located at the intersection of grain boundaries. At the same time, isolated micropores inside the grains are not excluded.
Hot pressing sintering equipment and molds
The hot pressing process usually uses electric heating. We can divide the pressurization operation process into maintaining constant pressure throughout the heating process, pressurizing only at high-temperature stages, and segmented pressurization (adding different pressures at different temperature stages) according to different sintering materials. The hot pressing environment atmosphere includes a vacuum, normal pressure protective atmosphere, and protective atmosphere conditions of a certain gas pressure.
Among the mold materials used for hot pressing equipment, widely use graphite. The price of graphite is not too expensive and it is easy to machine. It has a low density, low resistance, and good thermal stability in a large temperature range. It has sufficient mechanical strength and can form a protective atmosphere. The compressive strength of the graphite used in the actual die is 35~45MPa. Use the high-strength graphite under pressures of up to 70MPa. The limitations of graphite die-casting are its low mechanical strength (it cannot work under high pressure) and its ability to reduce certain materials, especially oxides. Graphite can also react with transition metals and amides and silicides of transition metals.
In addition to widely used graphite die-casting, metal die-casting, especially copper-based alloy die-casting. Mainly use metal stamping to make polycrystalline optical materials, such as magnesium fluoride, magnesium oxide, and lead selenide. Oxide and ceramic material stamping is rarely used because of its poor thermal stability, difficulty processing, and difficulty coordinating and compatibility with the material being pressed.
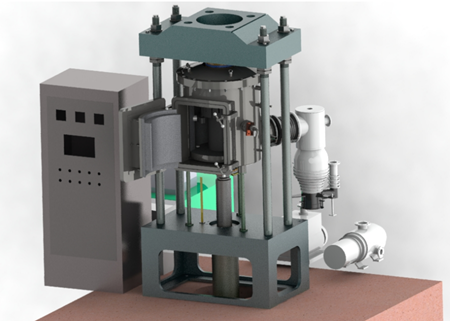
Characteristics of hot pressing sintering
- During hot pressing, since the powder is in a thermoplastic state, the deformation resistance is small and it is easy to flow plastically and densify. Therefore, the required molding pressure is only 1/10 of that of the cold pressing method. And it can form large-sized AlO3, BeO, BN, and TiB2 products.
- Since the heating and pressurization are performed at the same time, it is helpful for the contact, diffusion, flow, and other mass transfer processes of the powder particles. It can reduce the sintering temperature and shorten the sintering time, thereby inhibiting the growth of grains.
- The hot pressing method can easily obtain a sintered body with a density close to the theoretical density and a porosity close to zero. It is easy to obtain a fine-grained structure, and it is easy to realize the orientation effect of the crystal and control the composition change of the high vapor pressure component system. Therefore, it is easy to obtain products with good mechanical properties and electrical properties.
- It can produce products with more complex shapes and more precise sizes.
- The disadvantages of the hot pressing method are low productivity and high cost.
Back to SINTERING TECHNOLOGY
You might be interested in: